2020. 2. 29. 10:00ㆍ카테고리 없음
Determine the Series Type. (Comet Model Number)2. Measure the 'Outer Diameter' (O.D.) of the driven pulley on the jackshaft.3. Measure the 'Center Distance'; which is the exact distance between the center of the engine crankshaft and the center of the jackshaft or secondary shaft. Must be precise.4. Use the two measurements; the driven pulley outer diameter and center distance measurement to determine the correct belt part number from the relevant chart below.
Should your machine's center distance fall between the center distance settings listed here, select from the two belts, the one with the larger outside circumference (O.C.) for best wear and to avoid machine 'creep' during idling.Note: The Comet 20 Series and Comet 30 Series Driven Pulleys both have a #20 Stamped on them. Ignore the 20 Stamp completely, it's not a series indicator, it's the degree of the angle of the component.How To Install a Comet Belt. Remove the bolt and any keepers from the end of the engine crankshaft, and take the outer half of the clutch off. Clean the clutch. Make sure both components are perfectly aligned. Flat washers and shims are used as spacers.
Do whatever it takes to align both components so the side of the belt won't wear down prematurely and litter the system with belt debris. Align the sprockets so the chain will stay on. If you can install the belt without taking the clutch apart, the belt is too long.If the system is 'eating belts' do not install a new belt until the problem has been corrected. A damaged belt is the symptom of another problem.Some machines may require a different belt if the original engine has been replaced, which usually changes the center distance, or, if the original driven pulley has been replaced with a different outer diameter component.30 Series Belts Asymmetric 3/4' Wide. Comet Belts are not elastic and should not be viewed as a rubber band.
With the sophistication of drive belts and drive systems found in today's machines, the drive belt can do much damage to the entire system if the proper belt is not used or if the drive system is not properly aligned and adjusted. In earlier years, the drive system was considered a part of the machine that merely blew alot of belts. Many belts then were of the variety that if the drive system was not properly aligned and adjusted the belt would stretch and in most cases disintegrate before doing much damage to the clutch or driven unit.
Centrifugal Clutch Getting Hot
Today, however, emphasize belt and drive systems have attained such sophistication that if the drive system is not properly aligned or adjusted, or if the wrong belt is used, the belt may tear up the drive system before stretching or breaking. For that reason alone, and to eliminate the expense, trouble and possible safety hazard of blown belts or damaged clutches, the drive system on your vehicle should be given extra care to be sure it's operating properly. Basic guidelines are that the belt be checked periodically for uneven wear.

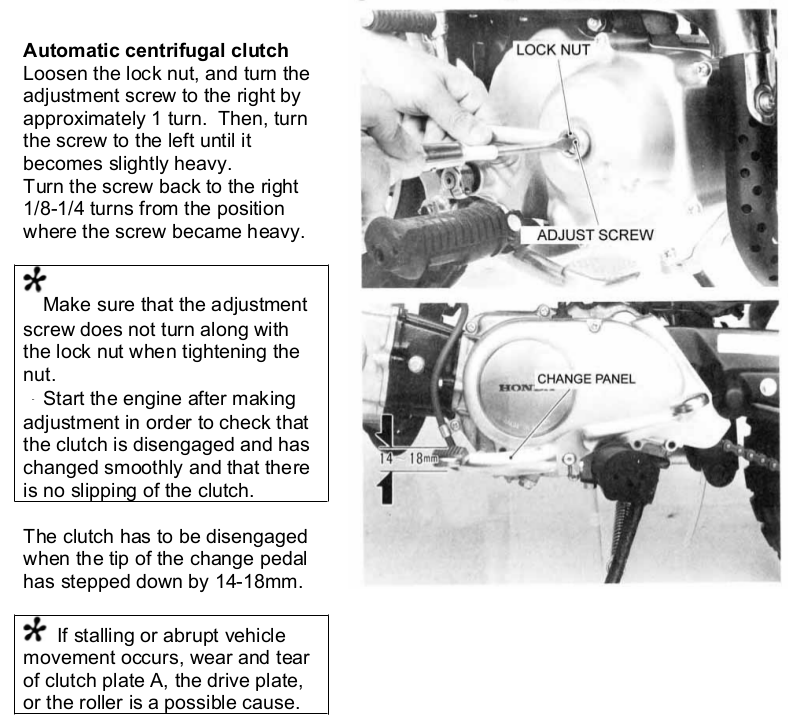
If any irregularities appear in the system or on the belt, have the system adjusted immediately.Check to make sure all of the black plastic cam buttons in the driven pulley are in place. Do not run the system if any of the buttons are missing.
Missing buttons will allow the driven pulley to open too far allowing the belt to fall down into an area of the pulley where rivets are present. These rivets will destroy the belt. The buttons also keep the movable sheave from spinning, they reduce friction between the cam and the movable sheave and they prevent metal to metal contact thus acting as shock absorbers.
How To Tell If Centrifugal Clutch Is Bad
The buttons play a very important role in the performance of a torque converter system. If you do have to replace buttons, glue the buttons into place with contact cement or a similar product.If your system is 'eating belts' do not install a new belt until the problem has been corrected. A destroyed belt is the symptom of another problem.Erratic engagement is most often caused by the driver clutch that is mounted on the engine crankshaft. The flyweights in the clutch are sticking or the movable sheave is binding on the hub.
Knowing how they work may help you determine why yours doesn't. As engine rpm increases, the flyweights push against the outer drum and force the movable sheave (pulley face) toward the engine causing the belt to travel at a greater circumference around the driver clutch. This action in turn causes the belt to force open the driven pulley, allowing the belt to travel at a lesser circumference around the driven pulley.As engine rpm decreases, the spring in the driven pulley closes the pulley forcing the belt to a greater circumference. This action overcomes the force of the flyweights against the movable sheave and causes the driver clutch pulley to open, allowing the belt to travel a lesser circumference around the driver clutch.When the engine is at idle, the driver clutch pulley should not engage the sides of the belt. The belt should be loose in the pulley and resting on the bronze bushing around the hub.
The bronze bushing serves to protect the belt from rubbing against the spinning hub at idle and also to support a portion of the movable sheave as the sheave moves toward the engine during engagement.The movable sheave must be able to slide freely on the splined hub without binding. Disassemble the driver clutch and clean away any dirt or lubricant residue using an automotive parts cleaning solvent. Do not use a petroleum based lubricant inside the driver clutch or between the hub and movable sheave.

Use a dry, molybdenum based lubricant. The extreme heat and pressure inside the driver clutch chars most petroleum based lubricants.
Petroleum based lube also collects dirt which causes increased wear. Graphite lube is better than petroleum lube, but it also eventually leaves a residue that builds up on the parts, causing them to bind and require more frequent cleaning.
Experience has taught us that works best.
I mounted a rototiller engine (Tecumseh TC300 or TC200 I think) on a bicycle after un-siezing every moving part on it, cleaning the carb etc. It seems to run well and starts very easy. But for some reason it won't make the bike move. When it's at full throttle the engine doesn't bog down or anything but smoke was coming from the centrifugal clutch and it didn't move the bike. The wheel on the bike spins if lifted off the ground but stops under any resistance. I don't think the gear ratio is to wide but that might be part of the problem. I think the clutch is not gripping well, but it looks exactly like the new one that I looked at.
There is no friction pad on the shoe, just steel on steel. Should I try cutting a cross-hatch into the shoes and drum of the clutch or is there a better way? Mabey something I'm overlooking?
UPDATE: The problem was the gear ratio. I have made it much narrower and the bike works now, but it has little torque espciaaly below about 5 mph. So I will make the gear ratio even narrower.